An overview of the proactive measures Artedomus is taking to reduce the environmental impact of our business.
By its very nature, the construction of our built environment consumes energy and resources, so it stands to reason that environmental sustainability has become arguably the most pressing issue in architecture and interior design around the world. We at Artedomus have been pleased to see so many Australian practices taking this a step further, by working to minimise the impact of not only the buildings they design, but their day-to-day business operations as well.
This holistic sustainability mindset has been part of Artedomus’s business since its inception. We’ve prepared this document to capture an overview of our efforts to minimise the impact of our business on the environment, our successes as well as our ongoing challenges.
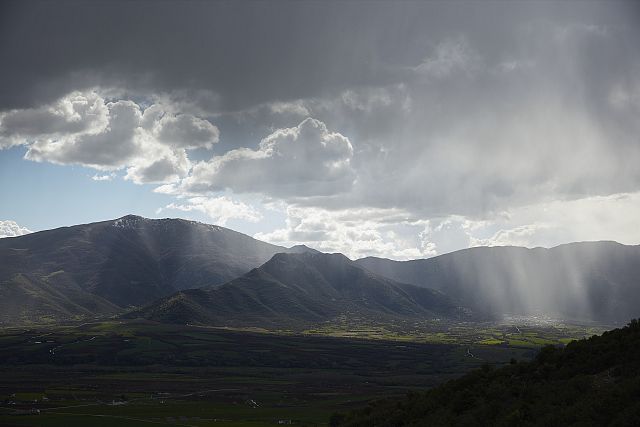
Administration, offices and showrooms
Two business-wide decisions immediately lowered Artedomus’s carbon footprint: switching to green energy for all of our eight business locations, and carbon offsetting all flights via our partnership with Greenfleet. In addition, we’ve installed 48 rooftop solar panels at our Brisbane showroom, Il Bosco Artedomus and we have also begun to move some of our vehicles across to be powered entirely by renewable energy. These measures build on a series of initiatives that have been developed over several years.
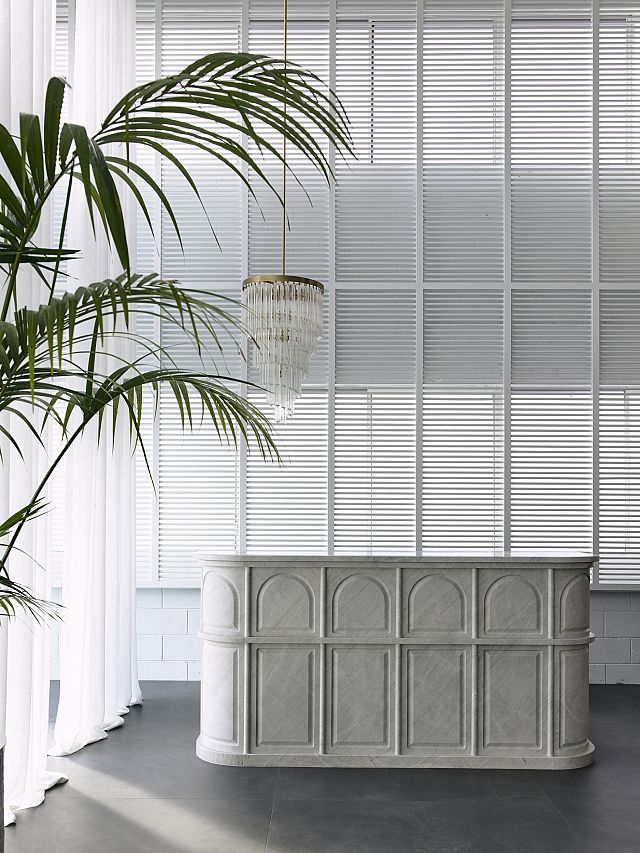
Reducing paper use
We’ve encouraged our staff to consciously reduce the amount of paper they use, and have removed the requirement for printing from as many processes as possible. Our sales and marketing team has supported this by actively ending the production of physical brochures and other paper-based promotional material, and requesting that our suppliers stop producing and sending brochures and publications to us. We’ve also removed all paper hand towel from our bathrooms, and where we do need to use paper, we’ve transitioned to the most sustainable options available. For example, our printers are stocked with recycled A4 and A3 paper, and we are sourcing toilet paper made with 100% recycled paper and no inks, dyes or scents.
A comprehensive recycling program
Over time, we’ve incrementally introduced measures for recycling all kinds of materials, and now run a comprehensive program for waste management that greatly reduces our contribution to landfill. Office documents and other printed matter are collected by an external provider for secure shredding and recycling; we have mixed recycling bins for common recyclable categories such as cardboard, cans, bottles and plastics; and we provide a separate bin to collect soft plastics. There are also separate bins at each location to collect used ink cartridges and batteries for recycling, and we have established protocols for the end-of-life handling of appliances, phones, computers, monitors, TV’s, cables as e-waste. Where Nespresso coffee machines are in use, there are containers for collecting the used pods for recycling.
Responsible material choices
The other consideration when supporting recycling initiatives is to stop using materials that can’t be reused or recycled, including for items that are sent out of the business. To this end, Artedomus has started using compostable mailers and has replaced bubble wrap with cardboard wrapping and packaging for all parcels and products samples. And to improve on this again, we’re performance-testing options for FSC-certified printable mailing labels, and paper-based adhesive tape. We’ve also removed single-use cups from all locations, instead providing Keep Cups as well as multi-cup carry trays for when coffees are purchased from cafes.
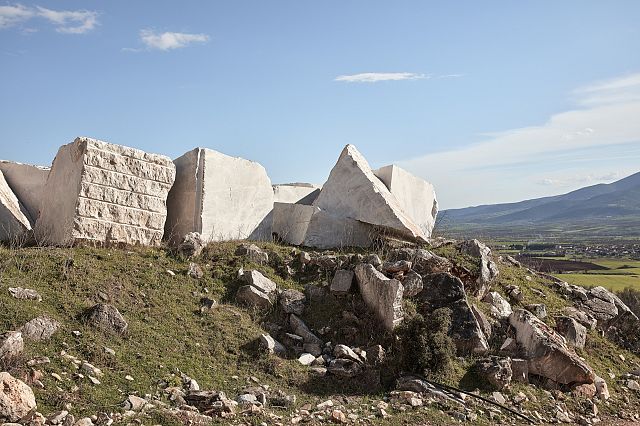
Warehouses and freight-handling
Many of the initiatives outlined above flow into our warehouses, but some have been adapted to account for the bulk handling of product and associated logistics. For example, in addition to the established mix of recycling receptacles, our warehouses have dedicated carboard-recycling bins to accommodate the larger volume of packing materials that arrive with product deliveries. Similarly, stone and tile waste, and old samples, are separated from other material and placed in a masonry bin for recycling. We have recently engaged timber recycling agencies in NSW and WA and continue to assess options for our other locations. In VIC and QLD we are-using A-Frames, cutting timber to size and reusing for various purposes within the warehouses or giving to others for the purpose of re-using the timber.
We’re working on further improvements to the ways we pack product for delivery, including performance-testing different plastic and corn-based wraps based on the sustainability of their recycling and disposal. We’re also working with our suppliers to ensure that the materials they use for packaging can be disposed of sustainably when we’re finished with them. In a recent positive outcome, our supplier of Elba marble has stopped using polystyrene as a packing material. And we’re currently coordinating with other overseas suppliers, and consulting with a local recycling company, to identify plastic wraps that can be recycled in Australia as soft plastics.
As with our offices and showrooms, the carbon footprint of our warehouses has been reduced significantly through the use of green energy and the carbon offsetting of all airfreight miles. We’ve also committed to replacing all forklifts and other vehicles at end-of-life with electric vehicles.
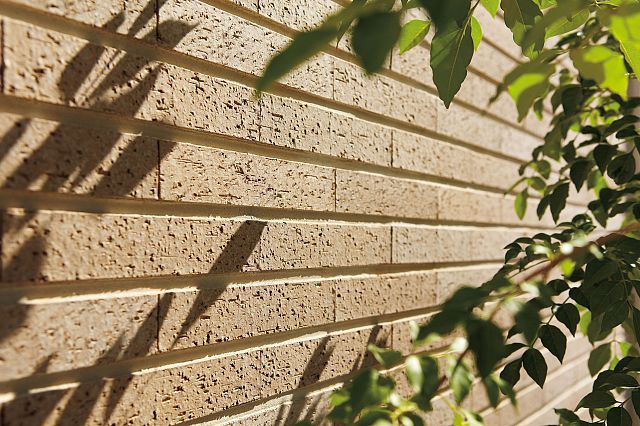
Supplier initiatives and product offering
Over the years, Artedomus has consciously partnered with manufacturers who not only make beautiful products, but share our values around sustainability. A good example is our Japanese ceramics supplier, Inax, whose manufacturing operations comply with ISO 14001 – Environmental Management Systems, meaning that they follow a comprehensive framework for environmentally responsible and sustainable business practices. And Fiandre, our Italian ceramics supplier, whose long-standing environmental commitment has even included developing proprietary technology to reduce the impact of their production processes, and then releasing it for use across the industry. Most recently, their sustainability efforts have coalesced under the ambition for zero VOC emissions from their ceramics kilns. A new Fiandre production facility will be established in Castellarano, in the province of Reggio Emilia, Italy and by the end of 2022 it will be equipped with native technologies enabling the use of green hydrogen in the production processes. This will make it the first ceramics factory in the world powered by green hydrogen renewable energy.
These business-wide initiatives are also reflected in the products that our suppliers make, and that we bring to market in Australia. There are specific innovations, such as Fiandre’s Active Surfaces photocatalytic porcelain, that is antiviral, antibacterial, reduces indoor nitrogen oxide and VOC levels. And Agape’s use of environmentally sustainable solid-surface material Cristalplant Biobased for the majority of their baths and basins. But also the broader qualities of products like porcelain and natural stone, manufactured without the harmful chemicals that we see in engineered and reconstituted stone products, and offering the sustainable life-cycle attributes of durability, longevity and recyclability.
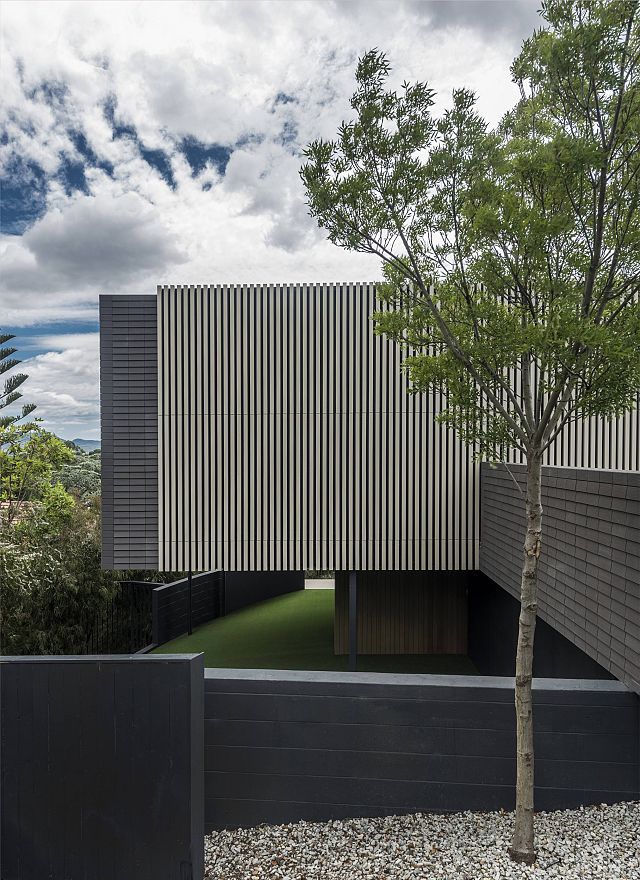